怎样提高焊接技术?必须要看的焊接缺陷及防治措施
焊接缺陷的种类很多,按其在焊缝中所处的位置可分为外部缺陷和内部缺陷两大类。外部缺陷也叫外观缺陷。
外部缺陷位于焊缝表面,借用肉眼或低倍放大镜就能观察到。
内部缺陷位于焊缝的内部,必须应用破坏性检验或专门无损检验方法才能发现。
焊接缺陷的常见分类方法如下:
二、焊缝尺寸不符合要求
1、现象
包括:焊缝外形高低不平、焊道宽窄不齐、焊缝余高过大或过小、焊缝宽度太宽或太窄、焊缝和母材之间的过渡不平滑等,如图1所示。
2、原因分析
(1)焊缝坡口角度、宽度及组装间隙不统一。
(2)焊条直径选择不当,造成填充层过高,失去坡口轮廓线,使盖面宽窄不一,焊缝过高,波纹粗劣。
(3)背面清根刨缝质量差,焊道宽度不一。
(4)焊接电流过大或过小,运条手法和角度不当以及焊速不均匀。
3、危害性
尺寸过小的焊缝,会降低焊接接头的强度;尺寸过大的焊缝,不仅浪费焊接材料,也会增大焊接结构的变形。焊缝金属向母材的过渡处若不平滑,出现尖角,会造成应力集中,降低焊接结构的承载能力。
4、预防措施
(1)采用自动和半自动切割机或刨边机加工坡口。
(2)焊缝组对间隙应控制在标准规范要求值以内,背面用碳弧气刨清根后,采用砂轮修整刨槽及碳化层,使刨槽宽窄一致。
(3)选用适当的焊接电流和焊条直径,遵守焊接工艺,熟练掌握操作技术,保持焊速均匀;手工焊操作人员要熟练地掌握运条速度和焊条角度,以获得成形美观的焊缝。
5、处理方法
对于焊缝余高过高,应用砂轮修整,宽窄不一或高度不够处,应重新补焊,且补焊连接处应圆滑过渡。
三、咬边
1、现象
咬边也称“咬肉”,是电弧或火焰将焊缝边缘的母材熔化后,没有得到填充金属的补充,而留下的凹陷或凹槽。
(1)焊接电流过大,电弧过长,运条角度不当及运条操作不熟练。(2)焊接运条时,坡口边缘两侧停留时间过短,造成熔敷金属与母材未熔合。(3)焊缝填充金属过低,盖面焊接焊肉过厚,电弧停留时间过长,焊缝区域温度过高而造成咬肉。
3、危害性
咬边是一种危险的缺陷,它不但减小了基本金属的有效工作截面,而且在咬边处还会造成应力集中。咬边又是一种常见的缺陷,应该特别引起注意。
4、预防措施
(1)选择合理的焊接工艺参数。碱性焊条应采用短弧焊接,保持运条均匀,坡口边缘运条稍慢些,停留时间稍长些,中间运条稍快些。多道焊中,应保持匀速焊接,应注意运条角度。
(2)焊条的填充金属应略低于焊道母材表面,这样盖面的焊道宽度轮廓清楚,外观成型好。
5、处理方法
焊缝咬边深度超标部分,应用砂轮打磨修整后补焊。对轻微咬边处用砂轮修磨成平滑过渡。
四、焊瘤
1、现象
熔化金属流淌到焊缝以外未熔化的母材上形成金属瘤。该处常伴有局部未熔合,有时也称满溢。习惯上,还常将焊缝金属的多余疙瘩部分称为焊瘤。
2、原因分析
(1)坡口边缘污物未清理干净;电流过大,熔池温度过高,使液体金属凝固较慢,在自重的作用下下坠而成;焊接速度太慢以及组对间隙太大等。
(2)运条角度不当,操作不熟练。焊速过慢也极易产生焊瘤。
3、危害性
焊瘤处应力集中,还易伴生裂缝等缺陷;焊瘤也破坏了焊缝平整光滑的外形,管子内部的焊瘸,除降低强度外,还减小管道的有效截面,造成堵塞观象。
4、预防措施
(1)焊接前应彻底清理坡口及其附近的脏物;组对间隙要合适;选择适当的焊接电流和运条角度,熟练掌握操作技术,保持焊速均匀。
(2)碱性焊条采用短弧焊接,极性反接。
5、处理方法
当出现焊瘤时,若伴有未融合、气孔、裂缝等缺陷时,应彻底清除缺陷,然后再进行补焊。对于焊缝金属的多余部分,可采用砂轮打磨的方法修整焊缝外形。在打磨时应注意观察内部是否伴有其它缺陷, 一旦发现伴生缺陷应彻底清除。
五、弧坑
1、现象
弧坑是焊接时,由于断弧和收弧不当,在焊道末端形成的低洼部分,表面低凹深度大于0.5mm以上。
2、原因分析
焊缝熔池金属未填足,熄弧过快或电流过大(薄板时)而造成。
3、危害性
弧坑低于基本金属表面,降低了焊接接头的承载能力,而且弧坑内常伴有气孔、夹渣、微裂纹等缺陷。4、预防措施
收弧过程中,焊条要在收弧处作短暂的停留或作回焊运条,使电弧不要突然熄灭、使焊条金属填满熔池。
5、处理方法
采用砂轮打磨修整、补焊,碱性焊条宜采用回弧焊接,以免引弧产生气孔。
六、飞溅
1、现象
手工焊接时,在焊缝及其两侧母材上产生一般性飞溅和严重性熔合飞溅。一般性飞溅是手工焊接常见的焊接质量通病;但产生严重性熔合性飞溅,其危害甚大,它会增加母材局部表面淬硬组织,易产生硬化发生脆裂及加速局部腐蚀性等缺陷。
2、原因分析
(1)碱性焊条使用极性不正确,电弧不稳定而产生飞溅。
(2)接地电缆接头不当,产生严重磁偏吹,造成严重飞溅。
(4)焊条保管不当,使其表面涂料变质外,更严重的是受潮,使内部含有大量气体引起的;
(5)选择电流过大,受潮的焊条内部含有大量的水份,在髙温熔解下,一部分水份被熔解在熔液中,在焊接电弧高温作用下,便熔解在金属的熔液气体发生剧热膨胀而胀裂,造成小粒熔液金属小滴落到焊缝及其两侧母材上。当温度不高时,小粒熔液金属冷却成一般性飞溅,当温度较高时,熔合在焊缝及其两侧母材表面的受热区域,称为熔合性飞溅。
3、预防措施
(1)加强焊条管理制度,使焊条不变质、不受潮。在库房的焊条应放置在通风良好、架空距地面高度不少于300~500毫米的高处;
(2)为了避免焊接产生飞溅,露天场合焊接施工时,在雨、露、雪等焊接潮湿环境,不采取有效防护措施,不得进行焊接;
(3)为了保证焊接环境,防止飞溅物产生,应适当提高温度,消除湿度。具体作法如下:
1)控制焊接环境的温度和相对湿度,当环境超标时应采取适当的防护措施,方可施焊;
2)焊前要清理坡口表面及其两侧不少于20mm范围内的水份、油污、铁锈等;
3)焊接材料(焊条、焊剂等)应有烘干和发放制度,焊条、焊剂的烘干温度和时间应严格按照相关要求进行。
4)烘干后的焊条应存放在100~150摄氏度的恒温箱中;现场施焊的焊工应具有良好的自动式焊条保温筒,焊条在保温筒内的时间不宜超过4小时,如超过时间应重新烘干。
5)对不锈钢及有色金属母材的焊接,为防止产生飞溅的缺陷,焊接时除了保证焊条干燥外,并在焊缝两侧母材金属表面涂刷防护涂料的保护措施或采用氩弧焊,可避免产生一般性或熔合性飞溅。
4、处理方法
对焊缝及其两侧母材表面产生一般性飞溅时,可用锉刀或手铲等工具除掉即可,如果属于熔合性飞溅时,可用砂轮打磨法彻底除掉,与焊缝母材相平(打磨深度不得超过0.5毫米)。
七、母材表面电弧擦伤(弧疤)
1、现象
电弧擦伤也叫弧疤或弧斑,多是由于偶然不慎使焊条或焊把与焊接工件接触,或地线与工件接触不良短暂地引起电孤,而在焊接工件表面留下的伤痕,形成许多小圆孔和凹坑。
2、原因分析
操作不慎,使焊条或焊把裸露部分与非焊接部位接触,短暂地引起电弧,将母材表面擦伤,形成许多小圆孔和凹坑。
3、危害性
电弧擦伤处由于电弧的短暂引燃与急速熄灭,冷却速度快,在易淬火钢及低温钢的工件上,会形成脆性淬硬组织,可能成为脆性破坏的起源点。
在不锈钢等有耐腐蚀性能要求的工件上,电弧擦伤会成腐蚀的起始点,降低材料的性能。
4、预防措施
(1)精心操作,避免带电的焊条或焊把裸露部分与非焊接区域母材相碰引起电弧。
(2)不得在非焊接部位随意引弧或试电流,引弧应在引弧板上或在焊道破口内进行。
(3)地线与母材应紧固良好。
5、处理方法
(1)对母材表面电弧擦伤磨除深度在标准要求范围内时,应用砂轮打磨平滑过渡。
(2)打磨深度超过标准要求时,应进行焊接修补。
八、气孔
1、现象
气孔是焊接熔池中气体在凝固时未能逸出,而残留在焊缝中所形成的空穴。根据孔穴产生的部位,可分为外部气孔和内部气孔;根据分布情况,气孔又可分为单个气孔、连续气孔和密集气孔等
2、原因分析
一切能导致焊接过程中产生大量气体的因素,如环境大气、溶解于母材、焊丝和焊条钢芯中的气体、焊条药皮熔化时分解产生的气体,焊丝和母材上的油污、水份、锈斑等脏物受热分解后产生的气体以及焊接冶金反应生成的气体等都是产生气孔的原因。主要是焊接材料和焊接工艺方面原因。
(1)母材表面及坡口处有水、油污、锈等污物。
(2)焊条受潮、药皮变质或脱落,钢蕊生锈。
(3)焊接电流过大,药皮发红、脱落造成保护失效,使空气侵入。
(4)碱性焊条引弧时,母材和焊条头部温度较低,焊条产生的保护气不足,熔池存在时间段,空气侵入熔池易产生密集气孔。
(5)运条操作不当,碱性焊条电弧过长,焊速过快,熔池存在时间短,气体来不及逸出。
(6)电弧产生偏吹。
3、危害性
存在于焊缝内的气孔,减小了金属的有效截面,从而使焊接接头的强度降低;气孔的边缘可能发生应力集中,密集气孔使焊缝组织疏松,使接头的塑性降低;贯通性气孔破坏了焊缝的致密性,造成渗漏。焊缝中的氢气孔还有可能导致裂缝的产生和扩展。
4、预防措施
(1)应将坡口及坡口附近15mm区域内的油污、油漆、氧化物、水分等污物清理干净。
(2)焊条应严格按照焊条说明书的要求进行焊条烘焙,不能以较低的烘干温度、较长的烘焙时间来代替,烘干后应恒温贮存,随用随取。用不完的焊条应及时回收,重新烘焙,烘焙次数不得超过两次,否则不能用于焊接。
(3)药皮开裂、剥落、变质、偏心过度以及焊芯锈蚀的电焊条不能使用。
(4)碱性焊条宜采用长弧回焊法引弧,长弧起预热作用,回焊可重熔引弧处,形成良好的保护气氛,消除缺陷。
(5)焊接时应避免风吹雨淋等恶劣环境的影响。室外进行气体保护焊时要设置挡风罩。焊接管子时,要注意管内穿堂风的影响。气体保护焊时,要注意气体的纯度和含水量必须符合有关标准的规定。
(6)选用适当的焊接工艺参数,碱性焊条极性应采用直流反接,电弧发生偏吹时,应及时调整焊接角度。
5、处理方法
(1)任何焊接质量缺陷在返修前都应查明原因,返修工作应由考试合格有相应资格的焊工来承担。
(2)焊缝表面缺陷,若深度不超过0.5mm时,只需用砂轮打磨处理,不需要补焊;若深度超过0.5mm时,则应予补焊,补焊后应磨光,磨光后的表面应光滑平整,均匀过渡。焊缝内部的超标缺陷,应根据探伤结果来确定缺陷部位,定好返修位置。
九、夹渣
1、现象夹渣是焊后残留在焊缝中的熔渣,有的夹在焊缝内部,有的夹在表面沟槽内。
焊缝中夹渣的来源:
(1)外界带入的夹渣:如母材中的夹渣混入到焊缝中;焊条药皮中的高熔点组分以及坡口边缘氧化物及渣壳等未清理干净,焊接时滞留在熔化金属中而造成夹渣;
(2)焊接过程中的冶金产物:焊接时进行的一系列冶金反应的生成物(氧化物、硫化物、氮化物等)在熔池金属凝固时来不及浮到熔化金属表面,而残留在焊缝中,即形成夹渣。
形成夹渣的原因是坡口角度小,焊接电流过小,熔池粘度大等使熔渣不能及时浮出 ;焊条药皮成块脱落后未被电弧熔化;多层多道焊时熔渣清理不干净;气焊时火焰能率不够,焊件清理不干净,操作时未将熔渣及时拨出等均会引起焊缝夹渣。
焊缝中夹渣的外形很不规则,大小相差也极悬殊。一般质量标准中,对点状夹渣的大小均有限制;对于条状夹渣,则应规定条状夹渣的长度、条状夹渣总长及条状夹渣间距的允许范围。
3、危害性
焊缝中的夹渣,降低了接头的承载能力,容易引起应力集中;影响了焊缝金属的致密性,还可能造成焊缝的渗漏,由于夹杂物与焊缝金属的线膨胀系数相差悬殊,温度剧烈变化时,有可能产生较大应力而导致裂缝。
4、预防措施
(1)选择合理的焊接电流,焊接时电弧不要压得太死,应利用电弧热量下方。使熔池达到和吹力使焊渣顺利地吹到旁边和淌到一定温度,防止焊缝金属冷却过快,以使熔渣充分浮出。
(2)焊接过程要始终保持清晰的熔池,铁水与熔渣应分得清楚,焊缝两侧电弧停留吋间长些,便于两侧沟槽的焊渣熔浮出来。
(3)各焊层的熔渣应清理干净,并修磨使焊道平整。
(4)使用合格的焊接材料。
5、处理方法
(1)任何焊接质量缺陷在返修前都应查明原因,返修工作应由考试合格有相应资格的焊工来承担。
(2)焊缝表面夹渣,若深度不超过0.5mm时,只需用砂轮打磨处理,不需要补焊;若深度超过0.5mm时,则应予补焊,补焊后应磨光,磨光后的表面应光滑平整,均匀过渡。焊缝内部的超标夹渣,应根据探伤结果来确定缺陷部位,定好返修位置。
十、未焊透
1、现象
未焊透是焊接时接头根部未完全熔化而留下的间隙的现象
单面焊根部未焊透
双面焊根部未焊透
2、危害性
未焊透降低了接头的机械性能,同时由于未焊透部位的缺口及末端会产生严重的应力集中,导致产生裂缝。
3、原因分析
(1)焊接电流过小或焊接速度过快,造成熔深过浅。
(2)坡口角度过小,钝边过大,根部组对间隙太窄。
(3)焊条操作角度不当,焊条偏吹,使电弧热源散失或偏于一侧,易造成另一侧产生未熔透。
(4)双面焊时背面清根不彻底,或氧化物、熔渣等阻碍了金属间充分熔合等。
4、预防措施
(1)根据规范要求控制坡口尺寸及组对间隙,彻底清理焊根,保证根部焊透。
(2)遵守焊接工艺,选择合理的焊接电流、运条角度及焊接速度,并注意根部熔化铁水,使用偏心焊条时,应注意调整焊接角度,使电弧处于正确方向。
(3)对于低合金钢材质,厚度大、导热快的母材,焊前一定要预热。
5、处理方法
在焊接质量标准中,双面焊或加垫板的单面焊中是不允许未焊透缺陷存在的。对于不加垫板的单面焊,允许的未焊透缺陷与焊缝的重要程度有关,重要焊缝不允许单面未焊透。应根据探伤结果来确定缺陷部位,定好返修位置。
十一、未熔合
1、现象未熔合是指焊缝金属和母材之间或焊道金属和焊道金属之间未完全熔化和结合的部分,它可以分为侧壁未熔合、层间未熔合和焊缝根部未熔合
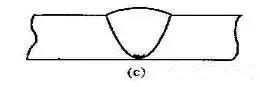
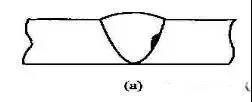
层间未熔合
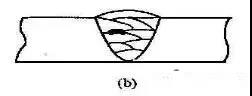
2、危害性
未熔合减少了接头承载的有效截面,降低了机械强度。
3、原因分析
(1)产生未熔合的原因是焊接线能量或火焰能率过小,即焊接电流过小或焊速过快,焊缝两侧运条停顿时间过短或焊条角度偏于一侧,使母材或层间金属未得到完全充分熔化,而被填充金属覆盖。
(2)母材坡口或前一焊道表面有氧化物或未清理净的熔渣等脏物时,焊接温度不够未能将其熔化结合时,也会形成未熔合。
(3)起焊温度低,焊速过快,易使焊缝始端未熔化。
4、预防措施
(1)选用合理的焊接工艺参数,运条角度和速度应适当,坡口边缘运条稍慢,停留稍长,使热量足以熔化母材和前一层焊缝金属。
(2)母材坡口内氧化铁及焊缝沟槽熔渣应清理干净平整。
(3)焊接中焊条有偏心时,应调整角度,使电弧处于正确方向。
5、处理方法
焊缝中一般不允许未熔合缺陷存在,当出现时,应根据探伤结果来确定缺陷部位,定好返修位置。
十二、裂纹
1、现象
在焊缝或近缝区,由于焊接的影响,材料的原子结合遭到破坏,形成新的界面而产生的缝隙称为焊接裂缝,它具有缺口尖锐和长宽比大的特征。
裂缝按其产生的部位可分为纵向裂缝、横向裂缝、弧坑裂缝、根部裂缝、熔合区裂缝及热影响区裂缝等,按其产生的温度和时间,又可分为热裂缝、冷裂缝和再热裂缝。
2、危害性
裂缝是一种危害最大的缺陷,除了降低焊接接头的承载能力,还因裂缝末端的尖锐缺口将引起严重的应力集中,促使裂缝扩展,最终会导致焊接结构的破坏。通常,在焊接接头中,裂缝是一种不允许存在的缺陷。一旦发现即应彻底清除,进行返修焊接。
3、原因分析及防治措施
由于裂缝的产生原因和形成机理的不同,下面就热裂缝、冷裂缝和再热裂缝三类分别予以讨论。
(1)热裂缝
热裂缝一般是指高温下(从凝固温度范围附近至铁碳平衡图上的A3线以上温度)所产生的裂纹,又称高温裂缝或结晶裂缝。
热裂缝通常在焊缝内产生,有时也可能出现在热影响区
热裂纹
焊缝中的纵向热裂缝一般发生在焊道中心,与焊缝长度方向相平行;纵向热裂缝一般沿柱状晶界发生,并与母材的晶粒界相联,与横缝长度方向相垂直;根部裂缝发生在焊缝根部,弧坑裂缝大多数发生在弧坑中心的等轴晶区,有纵、横和星状等几种类型。热影响区中的热裂缝有横向,也有纵向,但都沿晶粒边界发生。
热裂缝的微观特征一般是沿晶粒边界开裂,故又称晶间裂缝。当裂缝贯穿表面与外界空气相通时,热裂缝表面会出现蓝灰色等氧化色彩。有的焊缝表面的宏观热裂缝中充满熔渣。
产生热裂缝的原因是由于焊接熔池在结晶过程中存在着偏析现象,低熔点共晶和杂质在结晶过程中以液态间层存在形成偏析,凝固以后强度也较低,当焊接应力足够大时,就会将液态间层或刚凝固不久的固态金属拉开形成裂缝。
此外,如果母材的晶界上也存在有低熔点共晶和杂质,则在加热温度超过其熔点的热影响区,这些低熔点化合物将熔化而形成液态间层,当焊接拉应力足够大时,也会被拉开而形成热影响区液化裂缝。总之,热裂缝的产生是冶金因素和力学因素综合作用的结果。
防止产生裂缝的措施,可以从冶金因素和力学因素两个方面入手。具体来说有:
1)限制母材及焊接材料(包括焊条、焊丝、焊剂和保护气体)中易偏析元素及有害杂质的含量。特别应控制硫、磷等杂质元素的含量和降低含碳量。
硫几乎不溶于钢,它与铁生成低熔点的硫化铁(FeS)。焊接时,硫化铁的存在会导致焊缝热裂和在热影响区出现液化裂缝,使焊接性能变坏;同对硫以薄膜形式存在于晶界, 会使钢的塑性和韧性下降。磷也会使钢的塑性和韧性下降,提髙钢的脆性转变温度,并使焊缝和热影响区产生裂缝。一般用于焊接的钢材中硫含量应不大于0.045%,磷含量应不大于0.055%。有时还需要更严格的控制。
材料的焊接性能与含碳量密切相关。钢材含碳量越髙,焊接性能变差。一般认为,焊缝中碳含量控制在0.10 %以下,热裂缝敏感性可大大降低。
2)调整焊缝金属的化学成份,改善焊缝组织,细化焊缝晶粒,以提高其塑性,减少或分散偏析程度,控制低熔点共晶的有害影响。例如焊接奥氏体不锈钢时,采用奧氏体加铁素体的双相组织焊缝,可以提高其抗热裂性能。而单相奥氏体组织的焊缝,则容易产生热裂纹。
3)采用碱性焊条或焊剂,以降低焊缝中的杂质含量,改善结晶时的偏析程度。
4)控制焊接规范,适当提高焊缝的形状系数,采用多层多道焊法,避免中心线偏析, 可防止中心线裂缝。
焊接时,单道焊缝截面上焊缝宽度与焊缝厚度的比值叫焊缝的形状系数或焊缝成形系数。当焊缝的形状系数过小时,焊缝窄而深,低熔点杂质会聚集在焊缝中心,产生热裂缝的可能性大大增加,当焊缝的形状系数较大时,焊缝宽而浅,低熔点共晶和杂质聚集在焊缝近表面区,大大降低了中心线裂缝的倾向
形状系数对裂缝的影响
5)采取各种降低焊接应力的工艺措施,如采用合理的焊接顺序和方法、釆用较小的焊接线能量、整体预热和锤击法等。
6)收弧时填满弧坑,可避免产生弧坑裂缝。
(2)冷裂缝
冷裂缝一般是指焊缝在冷却过程中至A3温度以下所产生裂缝。形成裂缝的温度通常为300~200℃以下,在马氏体转变温度范围内,故称冷裂缝。
冷裂缝可以在焊接后立即出现,也可以在焊接以后的较长时间才发生,故也称为延迟裂缝。由于冷裂缝的产生与氢有关,也称氢致裂缝。冷裂缝的产生具有延迟性质,有可能造成预料不到的严重事故。因此,它具有更大的危险性,必须充分重视。
低碳钢和奥氏体不锈钢焊接时,冷裂缝倾向较小。而在焊接低合金钢、中碳钢及高合金钢等易淬火钢种时,则容易发生冷裂缝。
焊缝和热影响区均可能形成冷裂缝,如图13所示。焊道下裂纹常平行于焊缝长度方向并在热影响区扩展,不一定贯穿表面,有时呈连续状大致平行于熔合区发展。焊趾裂缝发生在焊缝和母材截面不连续处或咬边处等应力集中部位,在热影响区中扩展。焊趾裂缝产生在焊根附近或根部未焊透等缺口部位。
冷裂缝的特征一般无分枝,通常为穿晶型(相对于原奥氏体晶粒),但在不易淬火钢中存在混合组织时,有时也有晶间型。
形成冷裂缝的基本条件是:焊接接头形成淬硬组织;扩散氢的存在和浓集;存在着较大的焊接拉伸应力。这三个条件相互影响,相互促进。在不同情况下,三者中任何一个因素都可能导致冷裂纹的产生,其中扩散氢是诱发冷裂缝的最活跃的因素。
防止冷裂缝的产生主要从降低扩散氢含量,改善组织和降低焊接应力等方面采取措施。主要有:
1)采用碱性焊条或焊剂,减少焊缝金属中的扩散氢含量。碱性焊条又称低氢焊条,能降低焊缝金属中的含氢量;
2)焊条和焊剂在使用之前应严格按照规定的要求进行烘干。此外,还应仔细清理坡口和焊丝,去除油污、水份和锈斑等赃物,以减少氢的来源;
3)选择合理的焊接规范和线能量,如焊前预热、控制层间温度、焊后缓冷等,改善焊缝及热影响区组织状态;
4)焊后及时进行热处理。一是进行退火处理,以消除内应力,使淬火组织回火,改善其韧性;二是进行消氢处理,使氢从焊接接头中充分逸出;
5)提高钢材质量,减少钢材中的层状夹杂物,从结构设计和焊接工艺方面采取措施减小板厚方向上的焊接拉应力,可防止层状撕裂;
6)采取降低焊接应力的各种工艺措施(详见热裂缝,防止措施)。
(3)再热裂缝
再热裂缝起源于焊接热影响区的粗晶区,具有晶界断裂的特征。裂缝大多发生在应力集中部位。一般在焊缝区域再次受到加热时形成,故称再热裂缝。
产生再热裂缝的原因,一般认为是在再加热时,在第一次热过程中过饱和固溶的碳化物(主要是钒、钼的碳化物)再次析出,造成晶内强化,使滑移应变集中于原先的奥氏体晶界。当晶界的塑性应变能力不足以承受松弛应力过程中所产生的应变时,就形成再热裂缝。
在焊接工艺上防止产生再热裂缝的措施有:
1)减小残余应力和应力集中,如提高预热温度、焊后缓冷、使焊缝与母材平滑过渡等;
2)在满足设计要求的前提下,选择适当的焊接材料,使焊缝金属的高温强度稍低于母材,让应力在焊缝中松弛,可避免在热影响区产生裂缝;
3)在保证室温接头强度的情况下,提高消除应力退火温度,致使析出比较粗大的碳化物粒子,以改善高温延性。
免责声明:本文来源于互联网,版权归原作者所有,如涉及文章版权等问题,请及时与我们联系,我们将根据您提供的版权证明材料确认版权并删除内容!本文内容为原作者观点,并不代表本网站赞同其观点和对其真实性负责。